How to avoid bottlenecks in the layout of your industrial equipment?
The importance of a good machine layout to avoid bottlenecks in industrial processes
In any production process, efficiency is key to maximize productivity and reduce costs. However, one of the most common and damaging problems is the appearance of bottlenecks, which can be caused, to a large extent, by a poor arrangement of machines in the production plant.
What is a bottleneck?
A bottleneck occurs when a process or machine cannot handle the flow of work at the required speed, causing delays throughout the production chain. It is like a highway where one lane narrows, causing a traffic jam that affects all the vehicles behind it.
Consequences of bottlenecks
- Loss of efficiency: The production process is slowed down.
- Increased costs: More time and resources are required to complete production.
- Decreased quality: Delays can affect optimal process conditions, especially in sensitive industries such as biotechnology.
- Customer dissatisfaction: Delays in production can affect delivery time.
How does poor machine layout create bottlenecks?
- Lack of logical flow: If machines are not arranged according to the natural order of the production process, material may have to travel unnecessary distances.
- Tight spaces: Inefficient layout can lead to congested areas, making the movement of personnel and material difficult.
- Poorly located critical processes: If the slowest or most critical machines are at the beginning of the process, they can generate a domino effect of delays.
Practical example: Biotechnological processes
In a laboratory or plant using bioreactors and spray dryers, a poor layout could mean that the fermented product has to be transported through several unnecessary stations before it reaches the dryer. This is not only time consuming but can also jeopardize the quality of the product.
Solution: Efficient plant design
- Workflow analysis: Evaluate each step of the production process.
- Linear or U-shaped layout: Facilitate continuous material flow.
- Avoid crossovers and rework: Minimize unnecessary transport.
- Adequate space: Allow efficient movement of personnel and material.
At Techmi Group, we not only offer high-tech equipment such as bioreactors and spray dryers, but we also provide personalized advice to help you optimize the layout of your machines. Our goal is to make your production process smooth and efficient, avoiding bottlenecks and maximizing your profitability.
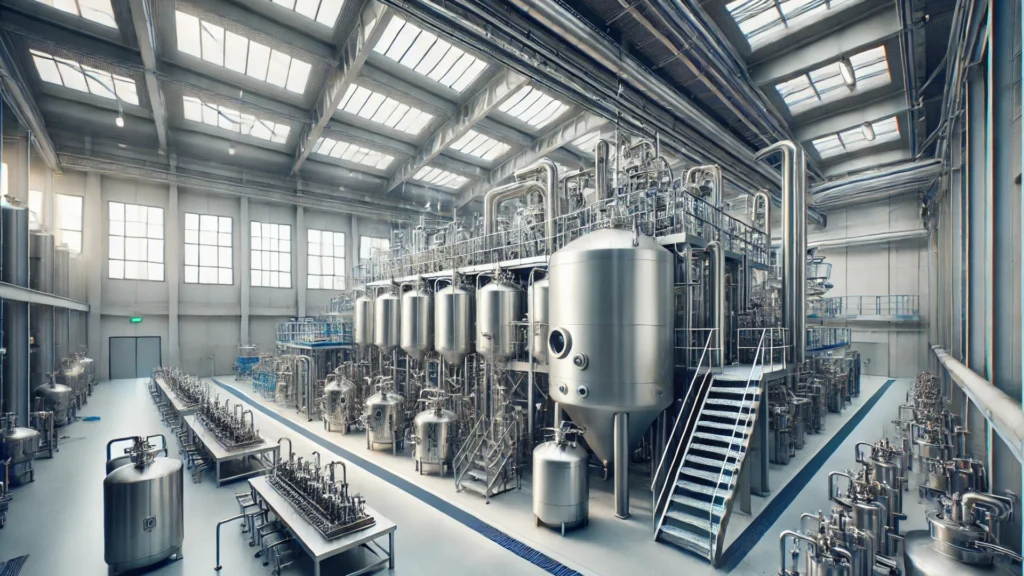
Are you ready to take your production process to the next level? Contact us and find out how we can help you.